Production
Perfect production planning for optimized processes
Scalable
Suitable for small to large production facilities
Cutting optimization
Great optimization thanks to smart algorithms
Compatible
Linkable to external ERP systems
Higher-level process optimization
Combined packaging optimization
About the Product
In conjunction with a more streamlined production process, you’ll find our software solution also flexibly configures production planning with various constraints, such as machines and processing sequences, all in an effort to improve your processes. Our software solution ensures optimized control over production batches, racks, and storage locations, employing state-of-the-art algorithms for precise waste optimization.
A+W Production offers flexibility and scalability, suitable for both small and large production environments. Compatible with various ERPs, it seamlessly integrates into existing systems, providing comprehensive production optimization solutions.
Unique cutting optimization algorithms guarantee maximum efficiency. Integration of capacity planning and production data acquisition enhances production control and processes.
Want to do more with A+W Production? Connect it to module extensions, such as the A+W Capacity Planner, A+W Barcode Manager, or A+W Production Terminal, which allow the system to scale and meet your newest needs and goals, so that the system grows with your company.
Functionalities and Benefits
- Plan and control production utilizing various restrictions, including machines, process sequences, etc.
- Quickly and easily manage orders and batches
- Optimize yield with state-of-the-art algorithms
- Sequence optimization as well as rack and storage space organization and optimization
- Optimization directly on racks and in boxes in shipping sequence (Software Module Extension: A+W Rack Optimizer)
- Visualization and modification of the cutting plan
- Simple machine management and direct machine control
- Efficient and graphical capacity planning (Software Module Extension: A+W Capacity Planner)
- Full integration of PDA and tracking (Software Module Extension: A+W Barcode Manager)
- Up-to-date statistics thanks to Crystal Reports and QLIK
- Printout production documents, bending texts, and barcode labels
With A+W Production, you have access to the latest production data and its current status allowing you to quickly react to changes and continuously improve. This software solution offers you a wide range of evaluation options to analyze and optimize your production processes.
Want to find out more about A+W Production? We will be happy to answer your questions and advise you on the best software solutions for your company.
Satisfied Customer Voices
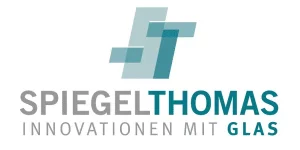
A+W Clarity Reference
Spiegel Thomas
The A+W programs digitize various processes, they tap various data silos, and therefore allow our machines to communicate with one another. Only this way is it possible for us to continue increasing customer satisfaction, further increase productivity and efficiency, and thus guarantee our delivery speed of up to 48 hours for TG.
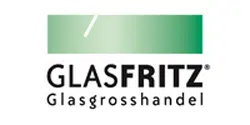
A+W Clarity Reference
Glas Fritz
The intelligent networking of our production through A+W Production has shortened delivery times by one to two days. Our staff who used to have to search for sheets and laboriously hand-pick them, now work productively. The process reliability has improved considerably and the error rate dropped to virtually zero.
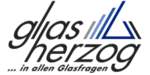
A+W Clarity Reference
Glas Herzog
A+W Business 6 is the best version of the commercial A+W software. The system works reliably, and thanks to the BOM concept, all products can be mapped. And if something gets hung up, A+W offers reliable service – our contact people, with whom we have been working for years, are experts, they help us quickly and easily.
Popular Add-ons
Clarity
Furnace Optimizer
A+W Furnace Optimizer introduces an intelligent solution for toughened safety glass production that aims to maximize furnace bed utilization and energy efficiency simultaneously. By reporting the availability of sheets prior to the glass tempering system, A+W Furnace Optimizer facilitates dynamic and efficient furnace bed occupancy.
This software solution conducts real-time optimization directly in front of the oven, ensuring cost-effective production based on available sheets. Providing a graphical display of furnace bed occupancy and seamless access to booked sheets, A+W Furnace Optimizer offers a user-friendly operation.
Integrated into the production data acquisition system, this software solution furnishes real-time production progress updates, thus enabling precise control of the furnace bedto optimize production processes and maximize machine utilization. With its dynamic, customizable functionality, emphasis on quality assurance, cost efficiency, A+W Furnace Optimizer emerges as the ideal solution for glass industry firms seeking to streamline production processes and bolster competitiveness.
- Graphic display of the furnace bed assignment for efficient monitoring
- Batch-by-batch production and booking of the furnace bed
- Online optimization directly in front of the furnace, based on the available sheets on racks
- Direct access to booked sheets on racks and slot carts via A+W Barcode Manager or A+W Production Terminal
- Ability to save and evaluate batch information in connection with A+W IoT - Smart Trace
Business
A+W Business is a complete ERP system for small and medium-sized companies. This commercial solution allows not just the entry of quotations, orders, credit notes, complaints, delivery notes, and the management of purchase orders and inquiries, but also control of other company areas (e. g. stock, purchasing, dispatch, etc.)
Business Pro
A+W Business Pro is a professional and cost-effective entry-level solution for small and medium-sized companies where order processing and production planning are completely integrated.
Enterprise
A+W Enterprise is a fully-integrated multi-site-capable ERP system for corporate groups and upscale medium-sized companies in the flat glass finishing industry.
Production
A+W Production is an extremely flexible PPS solution for complete rough and detailed scheduling for insulated glass, tempered glass, and laminated glass production. The system allows planning and control of even the most demanding multi-level production flows.
Clarity
Barcode Manager
Barcode scanning and tracking saves your employees and company time and money! A+W offers a wide array of functions to streamline production and process oversight.
Take charge of processing steps, keep track of machine utilization, and also record any breakage with ease using A+W’s barcode solution. This solution lays the groundwork for comprehensive evaluations and future planning, which are vital to your company’s current and future success. From status and storage location bookings (per user, station, machine, rack, item, and sheet) to precise processing entries and machine control via barcode scanning, our solution was designed to specifically meet your needs.
- Status and location bookings per user, station/machine, rack, item & sheet
- Machine start and control of processing via barcode reading
- Automatic reject handling (with implemented downstream concept)
- Statistical evaluations based on barcode readings (e.g. by using Crystal Reports or QLIK)
- Quality improvements based on breakage bookings
- Capacity updates based on barcode readings
- Printout of labels by A+W Production
- Flexible label design thanks to CR
- Centralized display of status information based on barcode readings by extension A+W Production Monitor and/or A+W Production Terminals
Business
A+W Business is a complete ERP system for small and medium-sized companies. This commercial solution allows not just the entry of quotations, orders, credit notes, complaints, delivery notes, and the management of purchase orders and inquiries, but also control of other company areas (e. g. stock, purchasing, dispatch, etc.)
Business Pro
A+W Business Pro is a professional and cost-effective entry-level solution for small and medium-sized companies where order processing and production planning are completely integrated.
Production
A+W Production is an extremely flexible PPS solution for complete rough and detailed scheduling for insulated glass, tempered glass, and laminated glass production. The system allows planning and control of even the most demanding multi-level production flows.
The A+W programs digitize various processes, they tap various data silos, and therefore allow our machines to communicate with one another. Only this way is it possible for us to continue increasing customer satisfaction, further increase productivity and efficiency, and thus guarantee our delivery speed of up to 48 hours for TG.
With the A+W Production system, we manage our complex product mix very flexibly. No more sheets are lost. And there are almost no complaints. We produce much greater quantities in the same amount of time. In addition, cutting has generally become more flexible and yield has increased significantly. The realtime optimization and automatic breakage pool also make a contribution here – poor sheets are remade immediately and can frequently still be delivered with the main order.
Clarity
Rack Optimizer
A+W Rack Optimizer transforms the packaging process in insulating glass production by enabling direct packaging and maximing the utilization of packaging materials. This ensures consistent packaging quality, while reducing reliance on employee expertise.
The software considers unloading sequences and allows for customized sequencing to balance weight and optimize rack loading/unloading, minimizing the needs for order picking and reducing transport costs A 3D visualization provides detailed previews and graphic instructions for packaging optimization.
- Increasing productivity on the IG line, addressing bottlenecks
- Eliminate re-sorting requirements in dispatch
- Potential use of robots for stacking and packaging
- Reduced breakage and rejects through automated glass packaging
- Automatic weight balancing and limit check for packing racks
- 3D pack view for detailed rack loading visualization and item identification
- Manual lite movement using the 3D pack view editor
- Special mode for cases
Production
A+W Production is an extremely flexible PPS solution for complete rough and detailed scheduling for insulated glass, tempered glass, and laminated glass production. The system allows planning and control of even the most demanding multi-level production flows.
Standalone
Solutions without ERP system
Clarity
Capacity Planner
A+W Capacity Planner provides a comprehensive overview of your production facilities’ available capacities and their utilization, which empowers you to effectively plan your production. This software solution also allows you to easily manage shifts, capacities, bottlenecks, and workloads for efficient processes.
This software offers flexibility in defining machine and operation restrictions, while also automatically adjusting production dates if capacities are insufficient. You can also calculate delivery dates, processing timelines, and costs effortlessly, while distributing loads across machines.
With A+W Capacity Planner, you can optimize production progress and costs by considering fixed processing times and campaign planning. By taking this information into account, you can reserve capacities and prioritize customer groups for streamlined order processing. Additionally, you can maintain control with detailed production progress displays and integration with A+W Barcode Manager and/or A+W Production Terminals. By being able to scale and combine A+W modules, you have more control and understand of every process in your facility.
- Display machine capacities and utilization information
- Easy management of shifts, capacities, bottlenecks and workload
- Free, formula-based machine and work process restrictions
- Automatically transfer production dates when capacity is insufficient at dispatch
- Calculate delivery dates and processing timelines
- Automatic calculation processing dates, durations and costs during import
- Automatic load distribution on machines based on work processes
- Cost calculation for orders and quotes
- Management of reservations and campaigns
- Directly communicate information to the ERP system
Business Pro
A+W Business Pro is a professional and cost-effective entry-level solution for small and medium-sized companies where order processing and production planning are completely integrated.
Production
A+W Production is an extremely flexible PPS solution for complete rough and detailed scheduling for insulated glass, tempered glass, and laminated glass production. The system allows planning and control of even the most demanding multi-level production flows.
With A+W iQuote, anything that is ordered can actually be built. The entire order runs through a restriction check based on master data stored in A+W Business. The customer transmits a technically correct complete order to us. There are no questions and time-consuming clarifications by telephone or e-mail. This is how we can achieve much greater efficiency in the entire order process.
Thanks to A+W Production and A+W Barcoding, the shop floor as well as the A+W Business order processing system know the processing status of every sheet, any time. The staff can answer customers’ enquiries right away on the phone – our customers appreciate this!